Digitalization in Poultry Farming: The Experience of Alel Agro
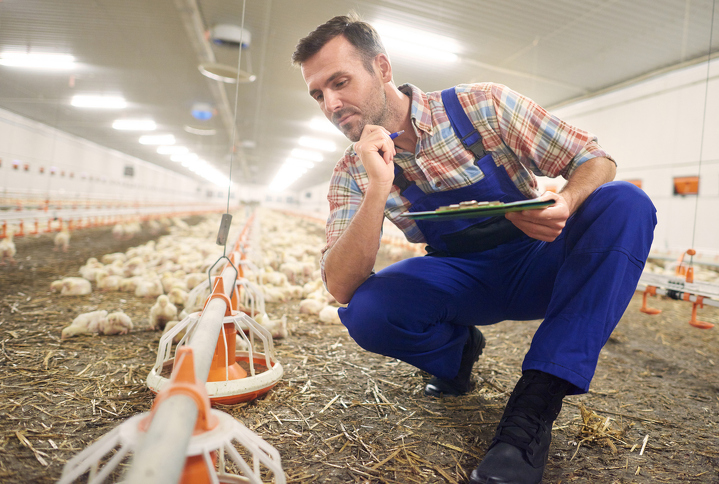
In July 2023, a significant event took place in Kazakhstan's poultry industry: the company "Alel Agro," which produces about 20% of the country's poultry meat, announced the full digitalization of its poultry farms. This means the company has succeeded in creating a unified information system that covers all aspects of the business, from poultry meat production to sales. The motivation for such an impressive technological leap was not a trend towards digitalization, but the necessity of the times. Growing competition and the need for rapid responses to numerous market challenges are motivating the largest players in the agribusiness industry to rethink business management models. This is why the management of Alel Agro was one of the first to turn to advanced "smart poultry" solutions.
The core of the new information system was a well-established ERP software product (Enterprise Resource Planning), which helps manage the company’s business processes. The implementation of all components of the unified information environment was entrusted to the leading Ukrainian developer "RASK. IN-AGRO." The representatives of the company and the IT developers shared their experience in automating a large poultry company.
Erik Sultankulov: "Without digitalization, you will move forward looking in the rearview mirror"
Recalling the difficulties of the digitalization process, the Chairman of the Board of Alel Agro, Erik Sultankulov, notes that the strategy for transitioning the business to "digital" was formulated not overnight. "It was important for us to understand how the digital ecosystem works. Especially valuable were trips around the world, during which we were able to study the experiences of leading poultry corporations in Russia, Europe, and America. Based on the knowledge gained and our existing experience, we developed a strategy for deploying a unified information environment for all our divisions," says the Chairman.
One of the main reasons that pushed the management towards business automation was the need for more dynamic business process management. The limited functionality of the accounting software and the significant amount of manual data processing became obstacles to decision-making and the implementation of new tools like cloud technologies, business analytics (BI), electronic document management, etc. These problems could only be solved through optimization and automation of the entire workflow.
The first leader is confident that paper documentation makes employees' work routine, not allowing them to free up energy for more interesting and productive work. The new ERP platform, on the other hand, organizes a comfortable and transparent environment for each system participant to control key poultry processes, as well as logistics, sales, and hundreds of other operations.
"Our old production management model provided limited, purely accounting information. But now, with the implementation of ERP, we can make management decisions based on both past and current data. Figuratively speaking, before we were driving the car while looking in the rearview mirror, but now we finally know what lies ahead," sums up Erik Sultankulov.
Tugluk Khodzhamiyarov: "The success of automation entirely depends on the level of employee training at the local level"
The IT Director of Alel Agro, Tugluk Khodzhamiyarov, talks about the technical side of digitalization. He is responsible for a wide range of issues related to the deployment of the information system, including creating technical specifications and interacting with the development team at all stages of the project.
Tugluk shares that, initially, a target digitalization architecture was created. This includes three major components: Smart Farm — intelligent control of poultry house microclimates, BI — business analysis software, and the ERP platform — business process management. Based on this, several important programs and services are built, particularly using artificial intelligence (AI), the Internet of Things (IoT), and machine learning (ML) technologies. All of these advanced solutions are integrated into a unified IT landscape of Alel Agro's digital ecosystem.
"We formulated the project charter, created resource and budget calendar plans. A great role was played by the steering committee, which included project managers and the company's first leader. Overall, we received full support for our initiatives from the management, and this positively affected the project timeline," shares Tugluk Khodzhamiyarov. Normally, ERP deployment takes at least a year, but in the case of Alel Agro, the developers managed to create a model of the future system in just six months, and another two months later, it was launched in pilot industrial operation. Currently, the ERP system is working fully, which allows calculating the cost of production, using business analytics (BI), and managing processes through a mobile application.
After the implementation of ERP and BI, a project to implement Robotic Process Automation (RPA) was launched. This technology uses software robots to take over routine business tasks, partially simulating user actions, which is why they are also called digital employees or twins.
Currently, the digital employee processes eight tasks within the company: searching for candidates for vacancies, meat subsidy applications, electronic invoice processing, reconciliation with retail networks, dealer bonus calculations, processing of procurement application cards, a bot for receiving payslips, and processing reconciliation acts for contracts. Everything that was previously done manually, and often with errors, can now be completed quickly, accurately, autonomously, and around the clock by the robot.
"The specifics of production are such that people at the local level are used to paper documentation and Excel. We understood that the efficiency of the new system would depend on employees' attitudes towards it. The problem was solved with several types of staff training, including process modeling. This allowed us to properly prepare people for the new working format," concludes the IT Director.
Andrey Ivanchikov: "It is important for the company's IT management to have leverage over the project"
Andrey Ivanchikov, co-owner and operational director of "RASK. IN-AGRO," talks about his experience working with Alel Agro. The company has been a leader in the agricultural digitalization market in Ukraine for many years; it’s enough to say that over 5,000 Ukrainian enterprises use "RASK. IN-AGRO" products for accounting automation.
"Our history in the Kazakhstan market began in 2010 when we were approached by representatives of 'Ivolga-Holding.' The new project interested us with its multi-faceted nature — the largest agro-industrial enterprise in Kazakhstan needed research and automation for the entire scope of activities, from agriculture to machine engineering," says Andrey Ivanchikov. After the first successful experience, new orders followed from Kazakhstani clients, such as projects for BI Group and ISKER holdings in the construction sector. Thus, by choosing Andrey Ivanchikov's team, Alel Agro not only gained leaders in automation but also specialists well-informed about the local market.
"Implementing an ERP system is a non-trivial task. According to global statistics, about one-third of all projects are considered unsuccessful and fail to meet their goals. Honestly, we didn't want to add to that sad statistic. Fortunately, in the case of Alel Agro, we had complete mutual understanding with the client. The client was ready to make non-standard and decisive decisions, and most importantly, to do everything on time. Moreover, both teams already had successful experience in similar projects, which ultimately led us to success," says the interviewee.
Recalling the difficulties of the project, Andrey highlights four factors that had to be taken into account in their work. First, it was the large and complex organizational structure of the client’s enterprise, which included branches and remote units. To solve this problem, a considerable number of specialists had to be involved, working in different locations and organizing their logistics. Second, the real challenge for developers was the process of replacing technologies in a large logistics warehouse, operating around the clock without days off. Equipment had to be replaced under conditions of continuous product dispatch.
Third, the project greatly expands the understanding of management systems, covering almost all of the client's processes — from poultry growing technology to client work using mobile applications. This affects the complexity of architectural and methodological solutions in the project. Fourth, the human factor. People have a hard time getting used to the new, unwilling to step out of their comfort zones. To address this, unique conditions had to be created to help employees adapt to the changes and the new system. Here, the leadership of the client company played a significant role, understanding the importance of working with people and responding to challenges in a timely manner.
"Working in Kazakhstan, with each project, we open up new facets of this wonderful country. The joint project with Alel Agro became such an inspiring discovery for us. In the near future, we want to promote the developed solution together. This is interesting in terms of replicating successful business products to other enterprises in the industry, both in Kazakhstan and other countries..." shares Andrey Ivanchikov.
Source: https://forbes.kz/articles/tsifrovizatsiya_v_ptitsevodstve_opyit_alel_agro